UA Tunnels Get Carbon Fiber Makeover
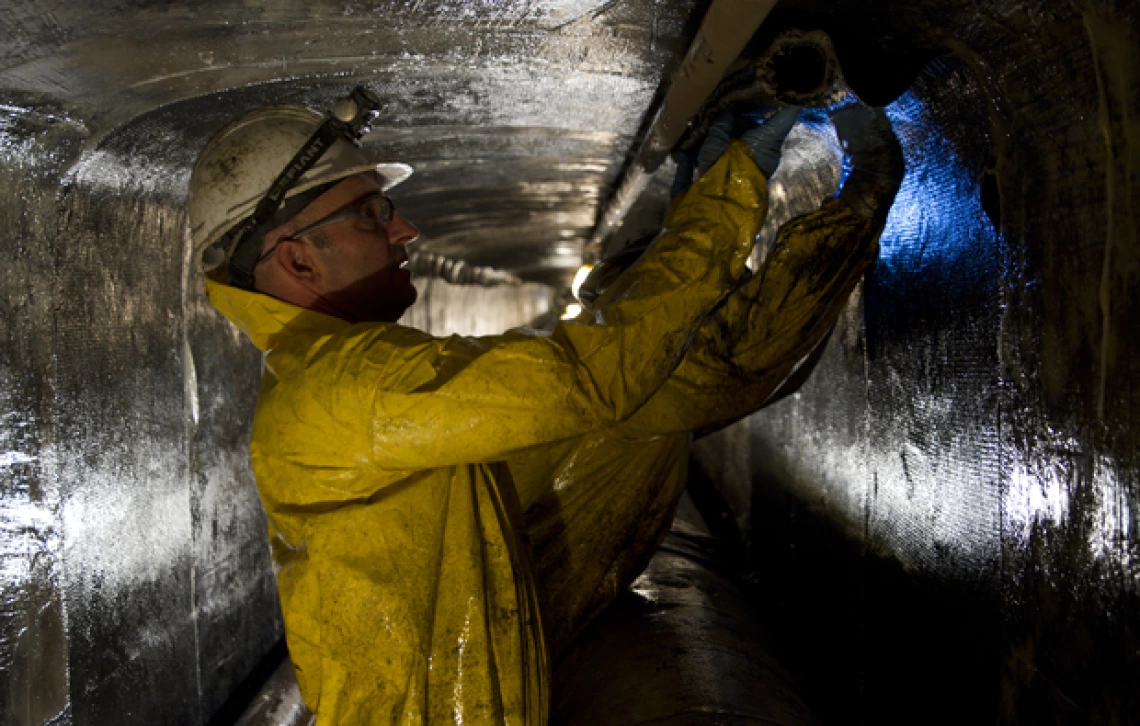
Article from College of Engineering website, and may be found here.
Ten feet beneath the pavement where students walk and bike on their way to class, workers clad in yellow protection suits, goggles and disposable gloves crowd inside a tunnel, attaching what appears to be wallpaper to the inside.
But the sheets they're tacking up are not paper and the adhesive they're using is not glue. They are affixing woven carbon fiber mats soaked in epoxy resin, which drips from the ceiling as they work. When it's dry, the layer they have applied will fortify the tunnel with a strength greater than steel.
Developed at the UA as a way of retrofitting buildings and structures against earthquakes, the carbon fiber lining is being used in a pilot project to restore and reinforce a utility tunnel that runs between the Student Union Memorial Center to the Chemical Sciences building, 850 feet across the Mall.
"We are applying carbon fiber-reinforced polymer to strengthen the tunnel ceiling," said Mo Ehsani, professor emeritus in the College of Engineering, who pioneered the concept of repairing and strengthening existing infrastructure with fiber-reinforced polymer in the late 1980s. "Even though these mats are applied like a fabric, they provide the equivalent of 1-inch steel bars placed a foot apart inside the tunnel."
The project came about through a collaboration involving UA Planning, Design and Construction, UA Facilities Management and Ehsani's company,QuakeWrap. The technology is a little bit like minimally invasive cardiovascular surgery: It allows construction crews to restore the vast network of utility tunnels that deliver water, electricity, steam and communication wiring to virtually every building on campus without excavating trenches and disrupting life above ground.
"Imagine the construction crews had to dig a trench through the Student Union, take all the dirt out and haul in fresh concrete," said Peter Dourlein, assistant vice president for Planning, Design and Construction. "Fixing the tunnel from the inside with QuakeWrap not only saves us money but is minimally invasive to our busy campus."
"We think it's a green solution, too," added Dourlein, explaining that compared with the conventional way involving the manufacturing and transport of concrete parts, QuakeWrap has a much smaller carbon footprint.
Some of the utility tunnels that crisscross beneath campus are 80 years old. Over time, water seeping into the ground and into cracks causes the concrete ceiling to deteriorate. As the reinforcement steel bars rust, they expand, widening the cracks in the concrete.
Saturated with epoxy resin, the carbon fiber sheets cure over the course of about a day and result in a rigid lining that is three to four times stronger than steel, said Ehsani, who served as a faculty member in the UA Department of Civil Engineering and Engineering Mechanics from1982 until 2010.
"The epoxy serves two functions: It distributes the load among the individual carbon fibers, which are microscopically thin, so they all participate in distributing the load. It also protects them against abrasion."
The concept behind QuakeWrap was first used on campus in 2007, when workers used fiberglass to repair the "thimble" that covers the optical testing tower of the UA's Steward Observatory Mirror Lab and protects sensitive instruments from the elements.
"We needed to find a cost-effective, quick and minimally invasive technology," said Chris Kraft,facilities project manager at Planning, Design and Construction, who oversaw the project. "QuakeWrap was by far the best long-term value. We met with Mo, reviewed his design and watched his crews wrap the thimble like an Ace bandage, making it stronger than new. All the while, a telescope mirror was being spun to perfection below without incident or interruption."
In another project, Quake Wrap was tested in tunnel south of the Physics and Atmospheric Sciences building in a collaboration that included Sundt construction company, GLHN Architects & Engineers Inc. and Turner Structural Engineering Company.
The results have been so promising that more projects are being planned, said Charlie Lynn, staff engineer at Planning, Design and Construction.
"We are very happy with the results so far," Lynn said. "QuakeWrap is another tool in our tool belt that we can use, and we love the fact it was developed here at the UA."
With funding from the National Science Foundation, Ehsani has developed another application that could revolutionize how pipes above or underground are being assembled around the world.
"We developed a way to manufacture pipes onsite to virtually any length without joints," Ehsani said.
Although still in the prototype stage, Ehsani's "endless pipeline" has received a lot of interest from potential clients. Instead of conventional concrete or steel, the new pipe consists of a central layer of lightweight plastic honeycomb, similar to that used in the aerospace industry, sandwiched between layers of resin-saturated carbon fiber fabric.
In combination, these materials are as strong, or stronger, than conventional steel and concrete pipes, which are time consuming and expensive to manufacture and transport. Concrete and steel pipes are built in short sections to fit on standard 18-wheel trucks, but Ehsani's new pipe can be built onsite as a single section of virtually infinite length, hence the product name, InfinitPipe.
The process starts by wrapping two or three layers of carbon fiber around a 20-foot-long core – called a mandrel – of the pipe's desired diameter, Ehsani explained.
"To give it rigidity, we put a layer of honeycomb material on the outside of the carbon fabric, and immediately on top of that, we wrap a layer of lower-cost glass fiber fabric," he said. "Next, ovens come down on the outside of the pipe to cure it. Once the nascent pipe has cured, we collapse the mandrel and pull it out of the pipe, but not completely. Two feet of pipe remain on the mandrel, and we'd wrap the remaining 18 feet with new fiber sheets. This process would be fully automated and repeat to produce pipe of the desired length."
The heavy industrial manufacturing processes, long-distance trucking and leak-prone joints used in steel and concrete pipe construction exact a heavy toll on the environment, not to mention the bottom line, which is why QuakeWrap is marketing InfinitPipe as the world's first "green" pipe.
"We anticipate to be able to produce roughly two miles per week," Ehsani said. "As this pipe is coming off the truck, it is already assembled. We can create about a foot of pipe every minute."